
TEC’s Core Business is the sale of plants (or licenses to build them) for the recycling of ELTs and technical rubber articles. TEC is following the authorization process to build an experimental plant (pursuant to Art. 211 of Legislative Decree 152/2006), in which the patented and already validated technology in the laboratory will be tested on an industrial scale. The plant will be built in Bari and will allow the treatment of up to a maximum of 5 tons of ELTs per day. Once the testing phase has been completed, the TEC team will be able to design, quote and sell ELT recycling plants worldwide (or related licenses), making use of the support of an EPC contractor for the construction. The very low emissions produced and the process logic aimed at closing the waste cycle according
to an approach aimed at the circular economy are in line with theglobal trend of environmental sustainability that is being pursued in Europe (and partly also in the rest of the planet). Given these premises and considering the need to dispose of enormous quantities of ELTs in an effective and green way (just think that 1.5 billion ELTs are produced every year in the world), there is a wide availability of the material entering the plant (also given the misalignment between supply and demand for ELT disposal), which is why we believe that TEC technology could find widespread application in the coming years, with possible plants located all over the world, as also confirmed by contacts and ongoing initiatives. The modularity of the main sections of the system can allow for easy sizing for any size of system that may be required.
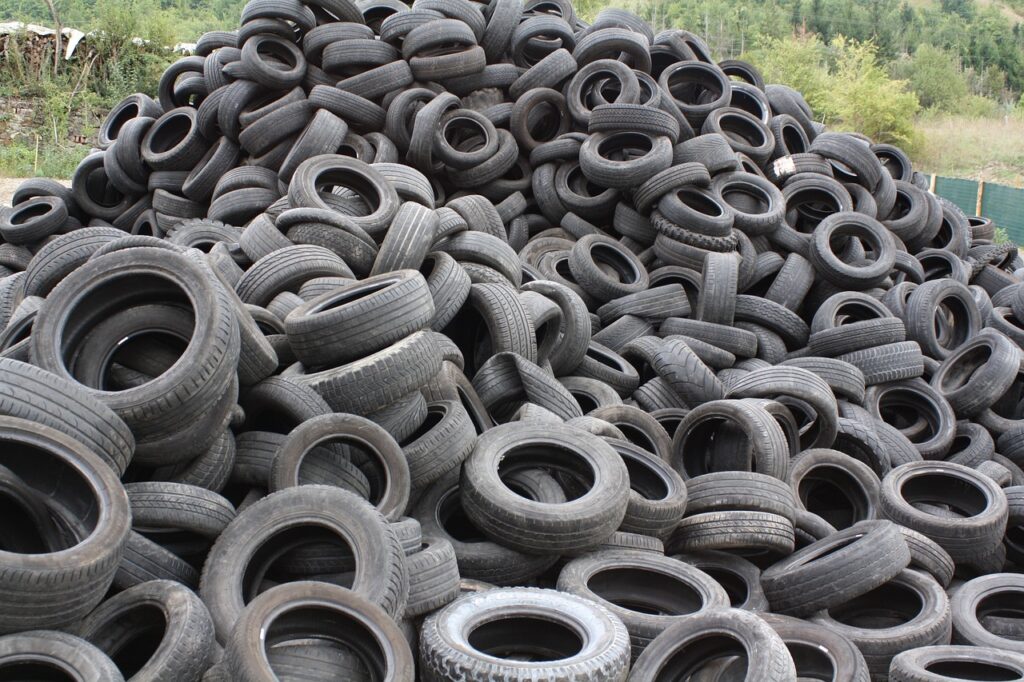
Recycling of materials from End-of-Life Tires (ELTs)
Every year millions of tons of tires exhaust their use cycle. The disposal of End-of-Life Tires (ELTs) occurs through:
– Landfill;
– Combustion (e.g. waste-to-energy plants);
– Mechanical crushing.
Steel, textile fibers and rubber granules are obtained from crushing. Rubber granules currently have few uses: they are only used in construction (asphalt, cement…), in some formulations of rubber compounds or as fuel.
Descriptions of the Macrophases of the Process
Storage
Shredding
Pyro gasification
Leaching
Pelletizing
Environmental benefits
- Reduction of CO2 emissions in support of Carbon Neutrality: the introduction of materials from ELT recycling into virgin compounds leads to a significant reduction in the carbon footprint compared to the starting compounds:
Virgin CB Carbon Footprint → 3,2 Kg CO2 e/Kg
Carbon Footprint CB from pyrolysis → 0,6 Kg CO2 e/Kg
The result is a Carbon Footprint reduction due to the replacement of CB with CBp → 80%
% of typical CB-Virgin compound → 30%
% CB-Virgo replaced with CBP → 100% (assumption)
It turns out one total Carbon Footprint reduction in the production of the compound* by replacing CB with CBp → 24%
* Considering only the raw materials used to produce the compound and total replacement of CB with CBp.
- Pyrolysis, used in the industrial PFU recycling cycle, has an insignificant environmental impact. It is not a combustion or incineration process but a thermal transformation into Hydrogen, carbon monoxide and light hydrocarbons. The process is self-sustaining thanks to the combustion of the syngas produced by the pyrolysis process itself and the excess syngas can be used to produce electrical or thermal energy to be used in the plant itself via a motor generator. This technology does not produce dioxins, PM10, polycyclic aromatic hydrocarbons, furans and benzofurans.
Technical benefits
-
- • The Carbon Black produced with the technology patented by TEC is purified from Polycyclic Aromatic Hydrocarbons (PAHs), harmful to humans and the environment, as well as from zinc, sulphur and transition metals. Another feature of the patented technology is the possibility of also removing silica and silicates and of controlling the morphology of the particles, improving their reinforcing effect in new compounds. The Carbon Black resulting from the process, called Fully recovered Carbon Black (FrCB), or Carbon Black from pyrolysis (CBp), can be used for the production of new tyres and in general of technical rubber articles, even potentially intended for direct contact with humans. The technology allows to obtain various types of Carbon Black with technical characteristics that overlap with those of different grades of CB furnace, which tyre manufacturers can use, in total or partial replacement of the CB furnace itself, in all parts of the tyre.
- In addition to Carbon Black, the metals embedded in the tyre compound are recovered, as well as synoil and syngas, which can be used as fuels.
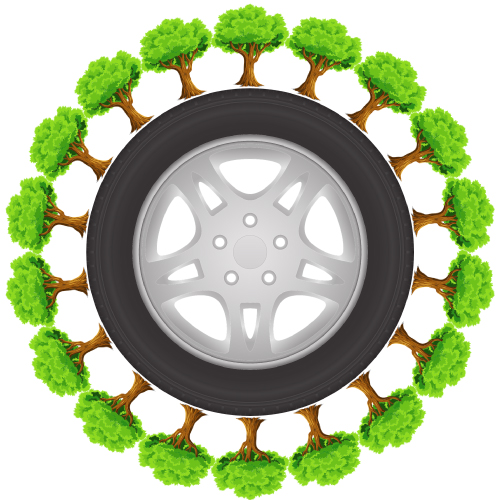
Environmental benefit
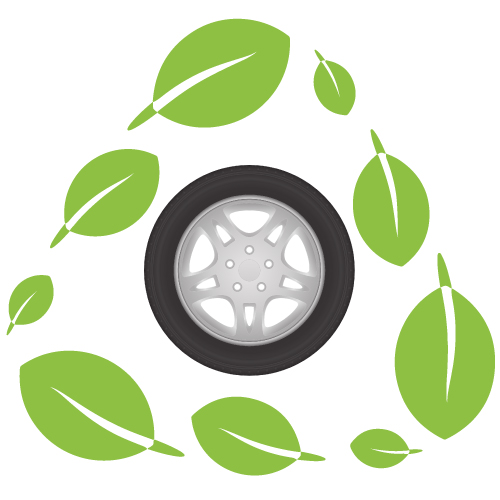
- The process perfectly follows the logic of the circular economy (recycling and reuse of resources), which the major global players in the sector are now focusing on.
- End-of-Waste products with high commercial value are obtained (carbon black, synoil, syngas, steel).
- Agreements with ELT disposal consortia are possible.
- At a global level there is an increase in sensitivity to the recovery of materials for the reduction of the carbon footprint, as confirmed by the efforts made in this sense by the main tire manufacturers, now “forced” by recent policies, mainly European but also global, to make its production more sustainable.
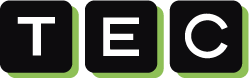
T.E.C. S.R.L.
Sede legale: Via Larga n.6, Milano (MI)
Sede Operativa: Viale Biagio Accolti Gil 26, Bari (BA)
Tel: +39 080 531 2316
Partita IVA 10564290962
2024 donaldmediagrafic